一、企業(yè)生產(chǎn)困境
該汽車制造企業(yè)擁有龐大且復(fù)雜的生產(chǎn)線,涵蓋沖壓、焊接、涂裝、總裝等多個(gè)環(huán)節(jié),各類設(shè)備來(lái)自不同供應(yīng)商,通信協(xié)議五花八門,如PLC之間的Profibus-DP、機(jī)器人控制系統(tǒng)的Ethernet/IP以及傳感器的Modbus RTU等。這就導(dǎo)致設(shè)備之間的數(shù)據(jù)難以共享,形成 “信息孤島”,生產(chǎn)管理部門難以及時(shí)、精準(zhǔn)掌握設(shè)備運(yùn)行狀態(tài),故障排查耗時(shí)費(fèi)力,嚴(yán)重制約生產(chǎn)效率提升,并且質(zhì)量管控也因數(shù)據(jù)滯后而存在漏洞,無(wú)法滿足日益嚴(yán)苛的市場(chǎng)需求。
二、工業(yè)通信網(wǎng)關(guān)選型與部署
為打破僵局,企業(yè)經(jīng)嚴(yán)謹(jǐn)評(píng)估,選用TDE具備多協(xié)議轉(zhuǎn)換功能、高可靠性工業(yè)通信網(wǎng)關(guān)。在部署環(huán)節(jié),依據(jù)生產(chǎn)線布局,于關(guān)鍵節(jié)點(diǎn)——各車間中控室及設(shè)備集中區(qū)域安裝網(wǎng)關(guān)。以沖壓車間為例,將網(wǎng)關(guān)與多臺(tái)沖壓機(jī)PLC連接,通過(guò)網(wǎng)關(guān)內(nèi)置的協(xié)議轉(zhuǎn)換模塊,把Profibus-DP協(xié)議數(shù)據(jù)轉(zhuǎn)換為統(tǒng)一的OPC UA協(xié)議,以便上傳至車間級(jí)MES系統(tǒng);在焊接車間,針對(duì)弧焊機(jī)器人與周邊輔助設(shè)備,網(wǎng)關(guān)實(shí)現(xiàn)Ethernet/IP到MQTT的轉(zhuǎn)換,確保機(jī)器人焊接參數(shù)、焊點(diǎn)質(zhì)量數(shù)據(jù)實(shí)時(shí)傳輸至云平臺(tái)供工藝工程師分析優(yōu)化。
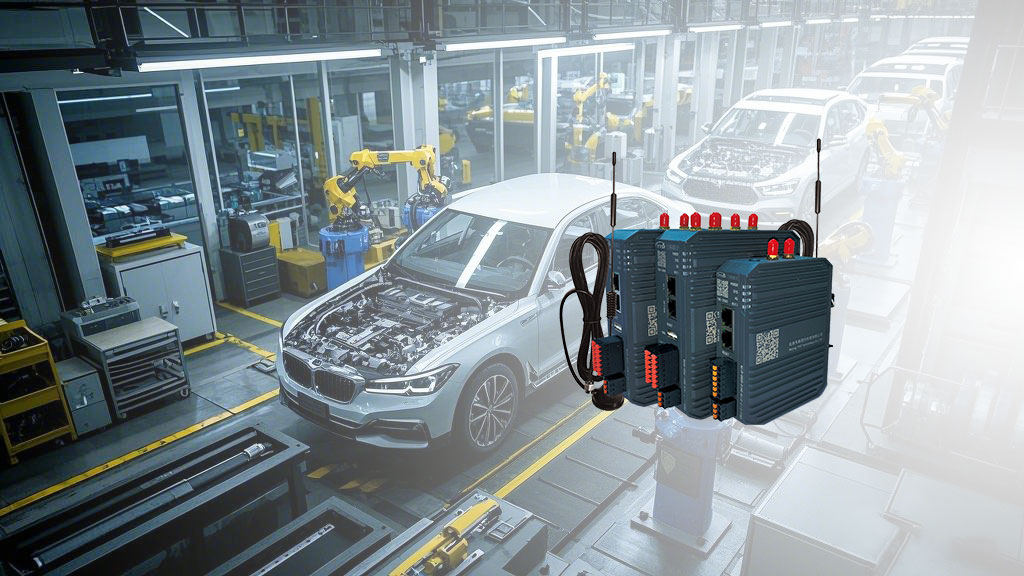
三、帶來(lái)的顯著效益
(一)實(shí)時(shí)生產(chǎn)監(jiān)控與調(diào)度優(yōu)化
部署通信網(wǎng)關(guān)后,企業(yè)管理層通過(guò)可視化大屏,可實(shí)時(shí)查看各車間設(shè)備開機(jī)率、產(chǎn)量、故障報(bào)警等信息。如總裝車間,一旦某條裝配線出現(xiàn)設(shè)備故障停機(jī),網(wǎng)關(guān)瞬間將故障信息推送至調(diào)度中心,維修人員能依據(jù)詳細(xì)故障代碼與位置迅速響應(yīng),平均故障修復(fù)時(shí)間從原來(lái)的2小時(shí)縮短至40分鐘,生產(chǎn)線綜合效率(OEE)提升15%,生產(chǎn)排期更精準(zhǔn),有效避免訂單延誤。
(二)質(zhì)量精準(zhǔn)管控
涂裝車間借助網(wǎng)關(guān)采集噴槍壓力、漆料流量、烘干溫度等工藝參數(shù),實(shí)時(shí)比對(duì)預(yù)設(shè)質(zhì)量標(biāo)準(zhǔn)范圍。一旦參數(shù)異常波動(dòng),立即觸發(fā)預(yù)警并反饋至工人終端與質(zhì)檢系統(tǒng),次品率從3%降低至1.5%,同時(shí)通過(guò)對(duì)歷史數(shù)據(jù)深度挖掘,優(yōu)化涂裝工藝參數(shù),提升漆面均勻度與光澤度,產(chǎn)品外觀質(zhì)量顯著提高,市場(chǎng)售后反饋故障率降低20%。
(三)預(yù)測(cè)性維護(hù)落地
通過(guò)長(zhǎng)期收集設(shè)備運(yùn)行數(shù)據(jù),如電機(jī)電流、振動(dòng)頻率、軸承溫度等,利用網(wǎng)關(guān)上傳至大數(shù)據(jù)分析平臺(tái),建立設(shè)備健康模型。以沖壓機(jī)為例,系統(tǒng)提前一周預(yù)測(cè)到關(guān)鍵零部件磨損風(fēng)險(xiǎn),安排預(yù)防性更換,避免突發(fā)停機(jī)造成的高額損失,設(shè)備維護(hù)成本整體降低10%,設(shè)備使用壽命延長(zhǎng)8%,為企業(yè)穩(wěn)定生產(chǎn)筑牢根基。